Destacking & Palletisation
You can keep production running smoothly by using the Destacking and Palletisation feature, which streamlines throughput at the saw by planning the off-stacking process. It gives you a list of pallet requirements or a baseboard cutting list and based on the size of your mechanised off-stacking stations will limit the number of open parts, ensuring finished items go to assembly as quickly as possible.
Highlights
- A station report provides information for conveying parts to the correct pallets or baseboards in the off-stacking area.
- A cutting list for baseboards is calculated from the part sizes allowing for oversize allowance, layout constraints and maximum stacking height.
- A destacking summary for the operator shows pattern by pattern on which pallet each part must be placed.
- The layout of parts on each pallet or baseboard can be downloaded to automatic off-stacking equipment.
- You can print labels for pallets or stacks when used with the parts and labels module.
- The destacking feature includes an advanced optimising algorithm which obeys maximum station sizes when allocating parts to stations.
In a recent installation of Magi-Cut, a special feature was implemented for a user who wanted to sequence production one job at a time, but allowed a changeover pattern to mix parts from two jobs.
Every job was treated as a 'pallet group', and the optimisation ensured that once a pallet group was started, it was completed before parts from another group were considered.
By allowing jobs to be processed in any sequence, and by allowing a mix of two jobs in a changeover pattern, an acceptable balance between yield and flow was achieved.
Printer friendly info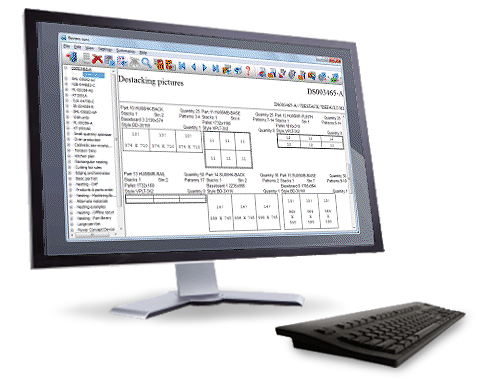